Just about everywhere you look lately, prices seem to be going up. That’s certainly no different in the propane industry. One of the biggest challenges for businesses today, in these times of high inflation and rapidly changing markets, is keeping track of your true operating costs and profit margins. Residential propane prices across the U.S. increased an average of 15% between October 2021 and March 2022, according to U.S. Energy Information Administration data.
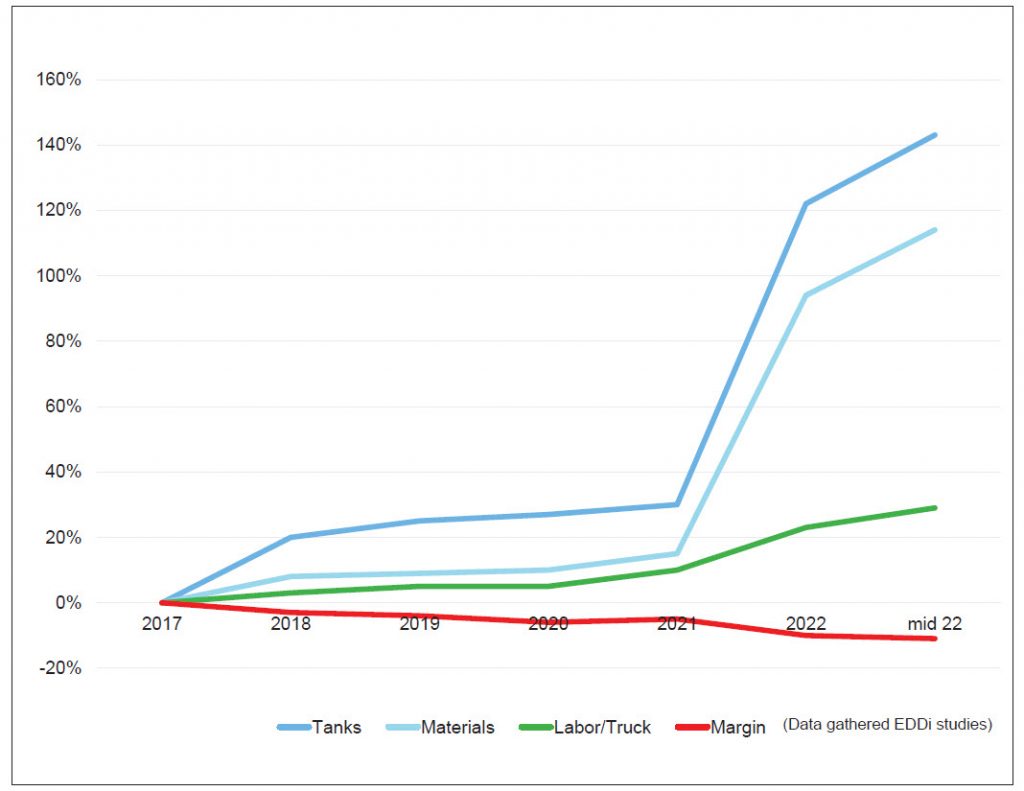
“Typically, retail price will follow product costs fairly closely, but historically, we have not seen the significant increase in asset costs at the same time,” says Dennis St. Aubin, CHS propane western sales director. “What we have seen in the past few years is that some operating costs have risen sharply, while margins have been on the decline.”
Since 2017, average margins for propane retailers have declined by 11%, according to information gathered by the CHS Energy Delivery Dialed-in (EDDi) Study. EDDi is a service offered by CHS Energy Distribution Solutions to help marketers explore opportunities for improved efficiency with their bulk refined fuel and propane businesses.
The first step in combating eroding margins is analyzing all operating costs and, in the case of recent years, understanding the impact to earnings if gross margins are set on a cents-per-gallon basis and have not kept pace with increased costs, says St. Aubin.
Tracking higher costs
Propane is an asset-heavy business. The cost of maintaining and expanding tertiary storage, bulk secondary storage and rolling stock has increased significantly over the past two years, thanks to increasing raw material costs.
Global steel prices have surged over 200% since early 2020, due to pandemic supply chain disruptions. The cost of new propane tanks is up 121% since 2017 and expected to increase another 22% by mid-2022, according to EDDi data. “A 500-gallon tank that cost 38 cents per gallon five years ago is projected to cost 72 cents per gallon by July of this year,” notes St. Aubin. “And there are currently significant delays to receive new tanks.”
The price of most equipment and materials has shot up, as well, with the price of copper pipe and fittings jumping nearly 300% the past two years. Overall material costs have nearly doubled, leading to major price increases for tank fittings and other installation products. Labor and truck costs have gone up an average of 20% since early 2021, according to EDDi data.
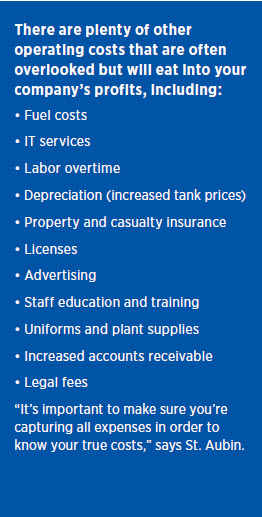
Boosting operating efficiencies
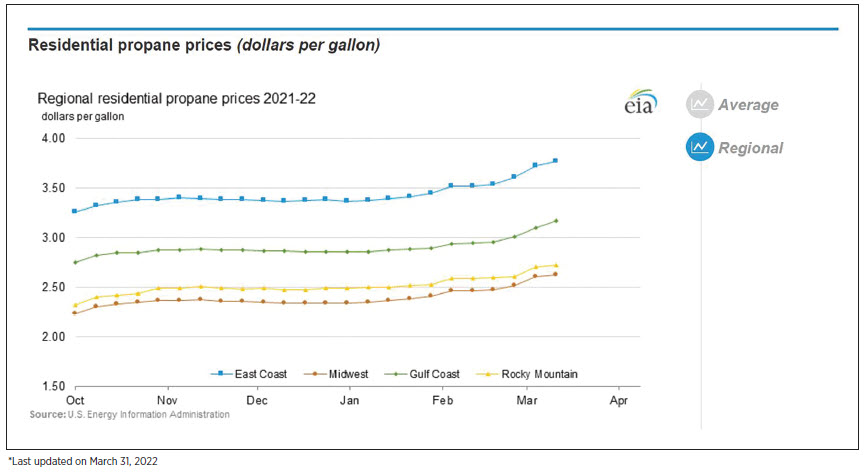
Once you know your costs to operate, you have to consider your historic returns and what
it will take to maintain a sustainable margin going forward, St. Aubin says. “When it comes to product pricing, are you testing the market? Will the market follow? Or are you watching the competition?”
“It’s definitely a balancing act, especially if you’re in a competitive marketplace,” he notes. “Competition can pull the market lower even when increasing costs should be pushing it higher.”
One solution is to track and improve your internal operating efficiencies, says St. Aubin. “Set benchmarks for efficiency measures, such as total gallons delivered, gallons per delivery, and tank-fill percentages and track them on a regular basis.”
He says that operational efficiency benchmarks will assist with controlling costs, and developing a growth strategy will set a plan for growing new gallons that best fits your company’s strengths.
Later this year, watch for new resources from CHS Propane to help your cooperative develop strategies to become more efficient and profitable.